Alum Helps Design and Manufacture Critical Items in the Fight Against COVID-19
Todd Goldstein ’08, director of 3D design and innovation at a New York City-area hospital system, has worked to print swabs and other medical devices in short supply during the pandemic.By: Meghan Kita Wednesday, June 17, 2020 00:30 PM
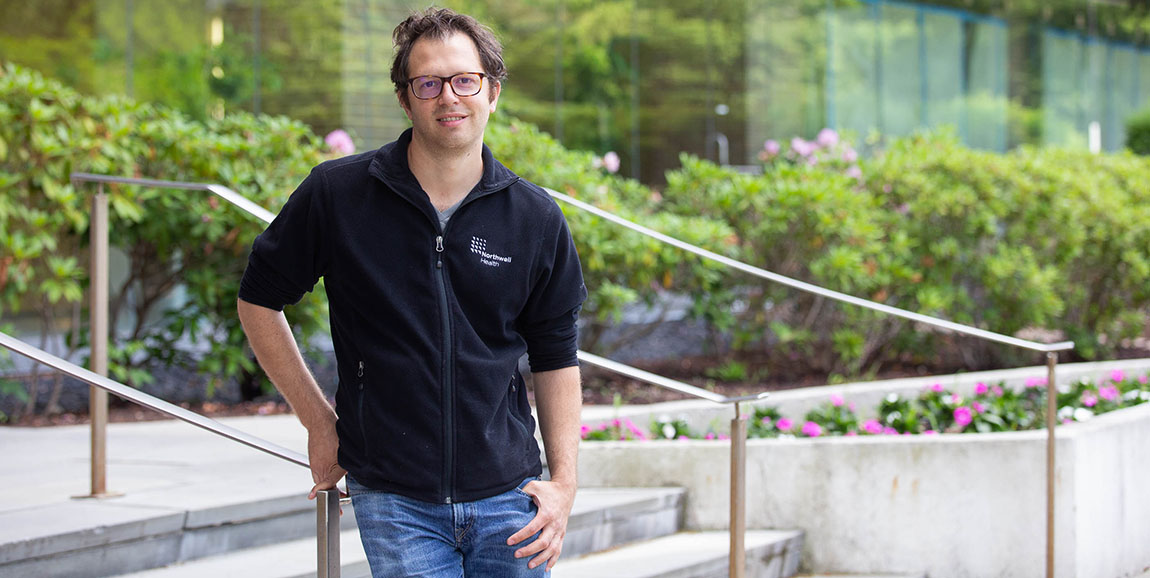
If someone had told Todd Goldstein ’08 in January what he’d be doing at work today, he says he would have asked if he got a new job. He hasn’t—Goldstein has been the director of 3D design and innovation at Northwell Health, a New York City-area hospital system, since his lab opened about three years ago. Prior to COVID-19, his lab made 3D models of complex problems—large tumors, severe fractures—to help surgeons simulate a procedure before actually doing it. They also created training models for medical students and prototypes for medical devices, among other tasks.
The pandemic put a halt to all elective surgeries, a term that encompasses even very urgent surgeries for diseases like cancer, and at first, Goldstein and his team weren’t sure what their role would be. Then, they started receiving requests to 3D print items the hospital was unable to order, including personal protective equipment and the nasopharyngeal swabs used to conduct COVID-19 tests.
Soon, a fear that the hospital system would run out of ventilators began to spread. Goldstein and his team designed an adapter that could be used to split ventilators between patients (which, thankfully, was never needed) as well as one that could convert bilevel positive airway pressure (BiPAP) machines into ventilators (which was—450 patients were treated in this way).
“We basically shifted from working on clinical cases to being professional problem solvers,” says Goldstein, who was a natural science major at Muhlenberg before earning a Ph.D. in biomedical engineering from the Donald and Barbara Zucker School of Medicine at Hofstra/Northwell.
The team’s largest project has been swab design and production to compensate for manufacturer shortages. In collaboration with a team from the University of South Florida’s Tampa General Hospital, they designed and printed swabs that were then put through a clinical trial to ensure accuracy. This trial happened quickly because so many local patients were being tested—200 of them agreed to be swabbed with the prototypes as well as conventional swabs, and Goldstein’s team compared the results.
Once the trial proved the 3D-printed swabs effective, the lab started manufacturing them for the health system. They’ve made more than 100,000 so far. They also released the design for other labs that have the capacity and materials to print their own; Goldstein estimates there are at least 20 health systems nationwide that could do it.
While the number of admitted COVID-19 patients has slowed, Northwell Health still isn’t permitting elective surgeries—only emergency surgeries and the most urgent of the urgent are currently allowed. All of those patients need to be tested frequently, so the availability of swabs remains critical. Everyone who enters the system’s facilities is required to wear a mask, and Goldstein recently received a request to design and test clear masks so hearing-impaired patients can read their providers’ lips. Masks like these exist, but the supply is low and the demand, due to COVID-19, is suddenly high.
“So many things have been on backorder,” Goldstein says. “We’re coming up with medical devices and testing them within days and weeks instead of the years it usually takes. We’ve shifted completely to being a design and production facility for medical devices.”